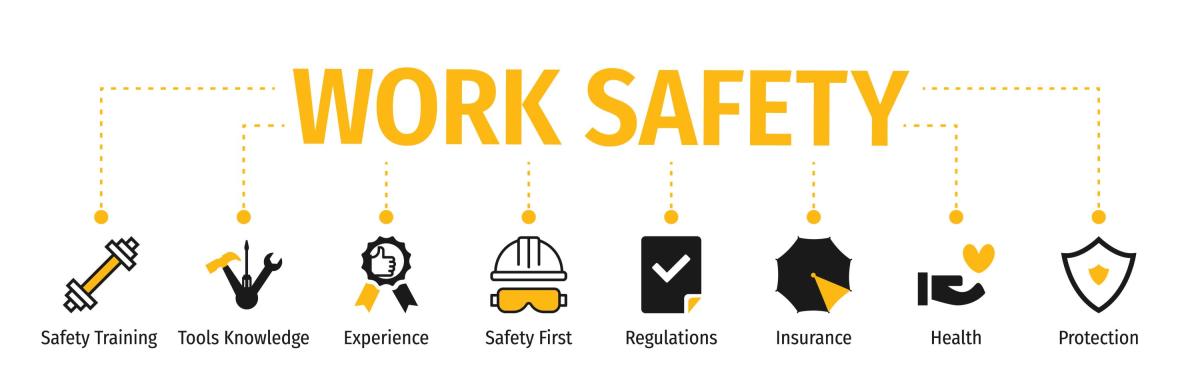
In today's rapidly evolving business landscape, workplace safety has become more critical than ever. As organizations strive to protect their most valuable asset—their employees—the importance of benchmarking against industry standards and adopting best practices cannot be overstated.
This comprehensive guide will explore how your business can leverage industry standards, comparative analysis, and emerging best practices to create a safer, more productive work environment.
The Power of Benchmarking in Workplace Safety
Workplace safety is not just a legal requirement; it's a moral imperative and a strategic business decision. Companies that prioritize safety often see improved productivity, lower insurance costs, and enhanced employee morale. However, to truly excel in workplace safety, organizations must look beyond their own walls and understand how they measure up against industry standards and their peers.
Benchmarking in workplace safety involves comparing your safety performance, processes, and strategies against established industry norms and the practices of leading organizations. This process helps identify areas where your safety program excels and where there's room for improvement. By understanding and implementing industry standards and best practices, you can create a robust safety culture that protects your employees and enhances your business's overall performance.
Understanding Industry Standards
Industry standards serve as the foundation for any effective workplace safety program. These standards, often developed by regulatory bodies, professional associations, and standard-setting organizations, provide a framework for implementing and maintaining safety measures across various industries.
Key Industry Standards to Consider:
Occupational Safety and Health Administration (OSHA) Standards: In the United States, OSHA sets and enforces safety standards for most private sector employers. Familiarize yourself with OSHA's General Industry standards (29 CFR 1910) and any industry-specific standards that apply to your business.
International Organization for Standardization (ISO) Standards: ISO 45001 is an international standard for occupational health and safety management systems. It provides a framework for improving employee safety, reducing workplace risks, and creating better, safer working conditions.
American National Standards Institute (ANSI) Standards: ANSI collaborates with industry experts to develop voluntary consensus standards across various sectors, including workplace safety.
Industry-Specific Standards: Depending on your sector, there may be additional standards to consider. For example, the construction industry follows OSHA's Construction Industry standards (29 CFR 1926), while healthcare facilities must adhere to standards set by organizations like the Joint Commission.
Importance of Aligning with Recognized Benchmarks:
Aligning your safety measures with recognized standards offers several benefits:
- Legal Compliance: Meeting or exceeding industry standards helps ensure your organization complies with relevant laws and regulations, reducing the risk of fines and legal issues.
- Risk Reduction: Industry standards are developed based on extensive research and experience. By following these standards, you can effectively identify and mitigate workplace hazards.
- Credibility and Reputation: Adherence to industry standards demonstrates your commitment to safety, enhancing your reputation among employees, customers, and stakeholders.
- Continuous Improvement: Standards often evolve to incorporate new knowledge and technologies. By staying current with these changes, you can continuously improve your safety practices.
Comparative Analysis with Peers
While industry standards provide a solid foundation, comparing your safety performance with industry peers can offer valuable insights and drive continuous improvement.
Methods for Peer Comparison:
- Industry Associations: Many industry associations collect and publish safety data from their members. Participating in these surveys allows you to benchmark your performance against similar organizations.
- Government Data: Agencies like OSHA and the Bureau of Labor Statistics provide industry-wide safety statistics, which can serve as a benchmark for your performance.
- Safety Conferences and Forums: Attending industry events provides opportunities to network with peers and learn about their safety practices and performance metrics.
- Third-Party Benchmarking Services: Some consultancies offer benchmarking services that provide detailed comparisons of your safety performance against industry peers.
Key Metrics for Comparison
- Total Recordable Incident Rate (TRIR): This measure the number of OSHA-recordable injuries and illnesses per 100 full-time employees.
- Lost Time Injury Frequency Rate (LTIFR): This tracks the number of lost time injuries per million hours worked.
- Near Miss Frequency Rate (NMFR): This measures the number of near misses reported per million hours worked.
- Safety Training Hours: Compare the average number of safety training hours per employee.
- Safety Observation Rate: This tracks the number of safety observations or audits conducted relative to work hours.
Benefits of Peer Comparison
- Identifying Areas for Improvement: Comparing your performance against peers can highlight areas where your safety program may be lagging.
- Setting Realistic Goals: Understanding industry averages and best-in-class performance can help you set ambitious yet achievable safety targets.
- Learning from Others: Discovering how other organizations have successfully tackled similar safety challenges can provide valuable insights and ideas.
- Motivation for Improvement: Seeing how you stack up against competitors can motivate your team to enhance safety performance.
Evolving with Emerging Best Practices
The field of workplace safety is continually evolving, with new technologies, methodologies, and insights emerging regularly. Staying abreast of these developments and integrating relevant best practices into your safety program is crucial for maintaining a leading-edge approach to workplace safety.
Technology Integration
- Wearable devices that monitor employee fatigue, posture, and exposure to hazards.
- Virtual and augmented reality for immersive safety training experiences.
- Artificial intelligence and machine learning for predictive safety analytics.
- Drones for safety inspections in hard-to-reach or hazardous areas.
Mental Health and Well-being
In recent years, organizations have begun to recognize mental health as a crucial component of overall workplace safety. This shift in perspective has led to significant changes in how companies approach employee well-being. Many businesses are now implementing comprehensive stress management programs and providing easily accessible mental health resources for their staff. Additionally, there's a growing focus on promoting work-life balance and offering flexible working arrangements. These initiatives aim to create a more supportive work environment, reduce stress-related incidents, and improve overall employee health and safety.
Safety Culture and Leadership
Developing a strong safety culture led from the top has become a priority for many organizations. Companies are increasingly integrating safety performance into leadership evaluations and compensation structures, emphasizing the importance of safety at all levels of the organization. This approach helps to ensure that safety remains a core value and is consistently prioritized. Furthermore, businesses are actively encouraging employee participation in safety initiatives and decision-making processes. By involving employees in safety discussions and improvements, companies can tap into valuable front-line insights and foster a sense of ownership in safety outcomes across the entire workforce.
Proactive Risk Management
The field of workplace safety is witnessing a significant shift from reactive to proactive safety measures. Instead of merely responding to incidents after they occur, companies are now focusing on preventing them before they happen. This approach involves the implementation of leading indicators to predict and prevent potential incidents. Organizations are also conducting regular safety audits and risk assessments to identify and address potential hazards before they result in accidents or injuries. By staying ahead of potential risks, businesses can create safer work environments and reduce the likelihood of workplace accidents.
Customized Training Programs
Safety training is evolving to become more personalized and engaging. Many companies are now developing safety training programs tailored to individual roles and risk profiles, ensuring that employees receive the most relevant and impactful information for their specific job functions. There's also a trend towards microlearning approaches for ongoing safety education, which involves delivering bite-sized, focused learning content that can be easily absorbed and applied. Additionally, some organizations are experimenting with gamification of safety training to increase engagement and retention of important safety concepts. These innovative approaches to training aim to make safety education more effective, memorable, and even enjoyable for employees.
Strategies for Staying Updated and Integrating New Practices:
Continuous Learning:
- Encourage safety professionals to pursue relevant certifications and ongoing education.
- Subscribe to industry publications and safety journals.
- Attend webinars, conferences, and workshops focused on workplace safety.
Networking and Collaboration:
- Join professional associations related to workplace safety.
- Participate in industry forums and discussion groups.
- Engage in partnerships with academic institutions researching workplace safety.
Pilot Programs:
- Implement small-scale pilot programs to test new safety technologies or methodologies.
- Gather data and feedback to assess the effectiveness of new practices before full-scale implementation.
Cross-Industry Learning:
- Look beyond your immediate industry for innovative safety practices that could be adapted to your context.
- Engage in cross-industry forums and collaborations to share insights and best practices.
Employee Feedback:
- Create channels for employees to suggest safety improvements and report concerns.
- Conduct regular surveys to gauge the effectiveness of current safety practices and identify areas for improvement.
Data Analytics:
- Leverage data analytics to identify trends, predict potential hazards, and measure the effectiveness of safety initiatives.
- Use dashboards and regular reporting to keep safety performance visible and top-of-mind for all stakeholders.
The Continuous Journey of Safety Improvement
Benchmarking your workplace safety against industry standards and best practices is not a one-time exercise but a continuous journey of improvement. By regularly assessing your performance against established standards, learning from peers, and embracing emerging best practices, you can create a dynamic and effective safety program that evolves with your organization and industry.
Remember that true safety excellence goes beyond mere compliance with standards. It requires a commitment to fostering a culture where safety is a core value, embraced by every member of the organization from the C-suite to the front line.
As you continue on this journey, consider the following action steps:
- Conduct a comprehensive audit of your current safety practices against relevant industry standards.
- Identify key performance indicators for safety and establish a system for regular benchmarking against industry peers.
- Create a roadmap for implementing emerging best practices that align with your organization's goals and challenges.
- Invest in ongoing safety training and education for all employees, emphasizing the importance of individual responsibility in maintaining a safe workplace.
- Establish channels for continuous feedback and improvement suggestions from employees at all levels.
- Regularly review and update your safety policies and procedures to reflect new standards, technologies, and best practices.
- Celebrate safety successes and milestones to reinforce the importance of safety in your organizational culture.
By taking these steps and maintaining a commitment to continuous improvement, you can create a safer, more productive workplace that not only meets industry standards but sets new benchmarks for excellence in workplace safety.
Remember, when it comes to workplace safety, the goal is not just to comply with standards or keep pace with peers, but to continuously strive for a zero-incident workplace where every employee goes home safe and healthy at the end of each day. Through diligent benchmarking, peer learning, and the adoption of best practices, your organization can become a leader in workplace safety, setting an example for others to follow.
At Northwest Safety & Risk Services, we're committed to helping businesses create safer work environments through our comprehensive consultation services, training courses, and occupational safety resources. Our team of experts stays at the forefront of industry standards and best practices, ensuring that we provide you with the most up-to-date and effective safety solutions. Whether you're looking to benchmark your safety performance, implement new safety initiatives, or enhance your existing programs, we're here to support you every step of the way. Remember, safety is an ongoing journey, and we're dedicated to being your trusted partner in making work safe.
For more information on how we can assist you in improving your workplace safety, explore our blog, attend our open-enrollment courses, or reach out to us directly. Together, we can create a culture of safety that protects your most valuable asset - your employees.
Sources:
OHSA - Recommended Practices for Safety and Health Programs
ASSP - Safety Is So Much More Than OSHA Compliance